“It’s a big Lego!” Inside Airbus’s manufacturing of the A350
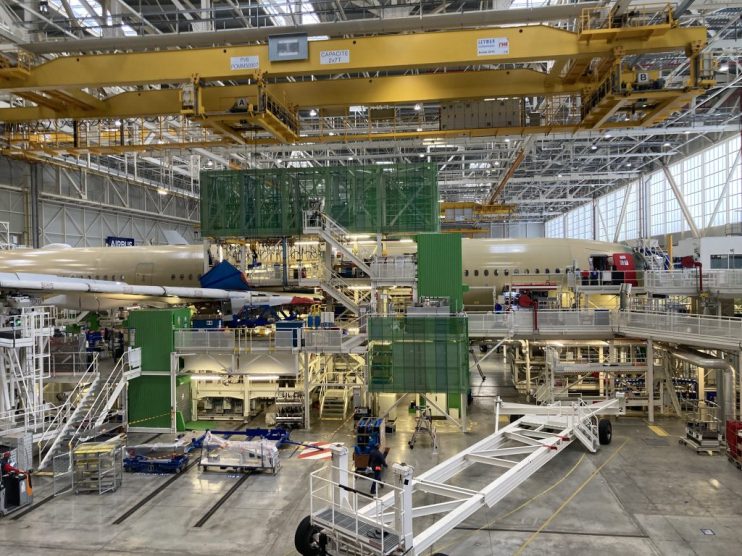
Plane maker Airbus is predicting that airlines will need 39,000 new planes built by 2040, as more travel for holidays and work and the need for replacing old and less-fuel efficient models increases.
The manufacturer has forecast that small aircraft such as the A320 will be the main drivers behind the demand, while around 4,000 orders will be made for the A350, the long-haul plane designed in 2004 to compete with Boeing’s 787 Dreamliner.
If you’ve ever boarded a Qatar, Singapore or Delta plane, chances are you have flown on an Airbus A350 aircraft. The model entered service for the first time in 2015 on a flight from Doha to Frankfurt, later becoming one the most-beloved long-range aircraft on the market.
To find out more about how the plane will be fundamental for the manufacturer’s post-Covid green recovery, I went to Airbus’s A350 factory in Toulouse.
Catherine Derunes Perez, who guided me through the factory, began the tour by telling me that making an A350 – which can seat between 315 and 350 passengers – is not more challenging than an A320.
Even though the process is the same, the amount of orders put forward greatly impacts production numbers. While the A350’s rate is at five per month, with hopes to get to six by the second quarter of 2023, targets for the A320 reach up to 65 per month.
“Even though the A320 is the best-seller, the A350 also sells very well, but of course they’re not meant for the same purpose,” Derunes Perez said.
A big Lego
While different parts for the aircraft come from France, Spain, Germany and the UK – the assembly line for the A350 begins in Toulouse, inside Airbus’s station 59 where staff, focusing on up to three planes at a time, work on installing monuments such as the galley.
“Airbus’s decision to work on modular stations does not block production,” she said. “If you have a delay on one aircraft you can continue to work on the others and you can go on without waiting for the production line to move.”
The A350’s segments are moved onto the next stage of production, where the fuselage sections are joined together and some parts of the electrical apparatus – including the nose landing – are connected.
“When Airbus assembles its aircraft, it goes rather fast,” she said. “They have to join the parts together but inside they just have to plug the electrical wires. It’s like a big Lego.”
The next step in the production process – which takes on average between four and five months from start to finish – is to install the wings and the tail planes, and only after that the aircraft is ready for testing.
“They have to examine everything they’ve done during the assembly, including checking the landing gear, all electrical and hydraulic connections,” said Derunes Perez.
The plane is later moved to a nearby plant, which is used to assemble the A330. More tests – including cabin pressurisation and fuel – are run.
Once the A350 is hand-painted, the engines and the furniture are all installed, the aircraft is ready for the test flight centre.
“At the flight test centre, they perform more than 150 hours of flight before delivering the aircraft, but when the customer comes to pick it up, the pilots need to perform an acceptance flight to check the aircraft behaves correctly and corresponds to what the customer has asked” she said.
A part of Airbus’s green recovery
After 18 challenging months that forced the manufacturer to axe production by 40 per cent, Airbus performed better than expected in the first half of 2021, raising its forecast for the full year.
With revenues going up 17 per cent year-on-year, Airbus performed better than its longstanding rival Boeing, which registered a 8 per cent increase. The companies made the headlines in June when they announced a halt to their 17-year feud.
Airbus’s positive results were in part due to financial restructuring and compromise deals the European plane maker had to strike to stay afloat during the Covid-19 pandemic.
“We had to adapt every assembly line and our rate and discuss with all our suppliers to make sure everyone was on the same page,” a company spokesperson told City A.M.
Despite the many challenges, consumer pressure highlighted a need for a new generation of fuel-efficient planes.
Commenting on future demand, Airbus’s chief executive Christian Scherer said: “The world is expecting more sustainable flying and this will be made possible in the short-term by the introduction of most modern airplanes.”
“Powering these new, efficient aircraft with sustainable aviation fuels (SAF) is the next big lever. We pride ourselves that all our aircraft – the A220, A320neo Family, the A330neo and the A350 – are already certified to fly with a blend of 50 per cent SAF, set to rise to 100 per cent by 2030.”
Green fuels are not the only focus of Airbus’s net-zero strategy. The company has in fact been developing a new generation of hybrid-hydrogen aircraft, ZEROe, that could enter service as early as 2035.
“We are clear we want to get to net-zero emission by 2050, and we are working to find the right partners [for ZEROe],” the spokesperson told City A.M.